Our know-how
At Nova Ride, everyone plays their part, from the first sketches to the shipping of the finished product.
Components designed with passion and transparency, this is our DNA. That's why we pay meticulous attention to every detail to offer you high-performance and durable products.
Our priority is to provide you with all the information you need to make the best choice. Discover the know-how of the team behind each of our products.
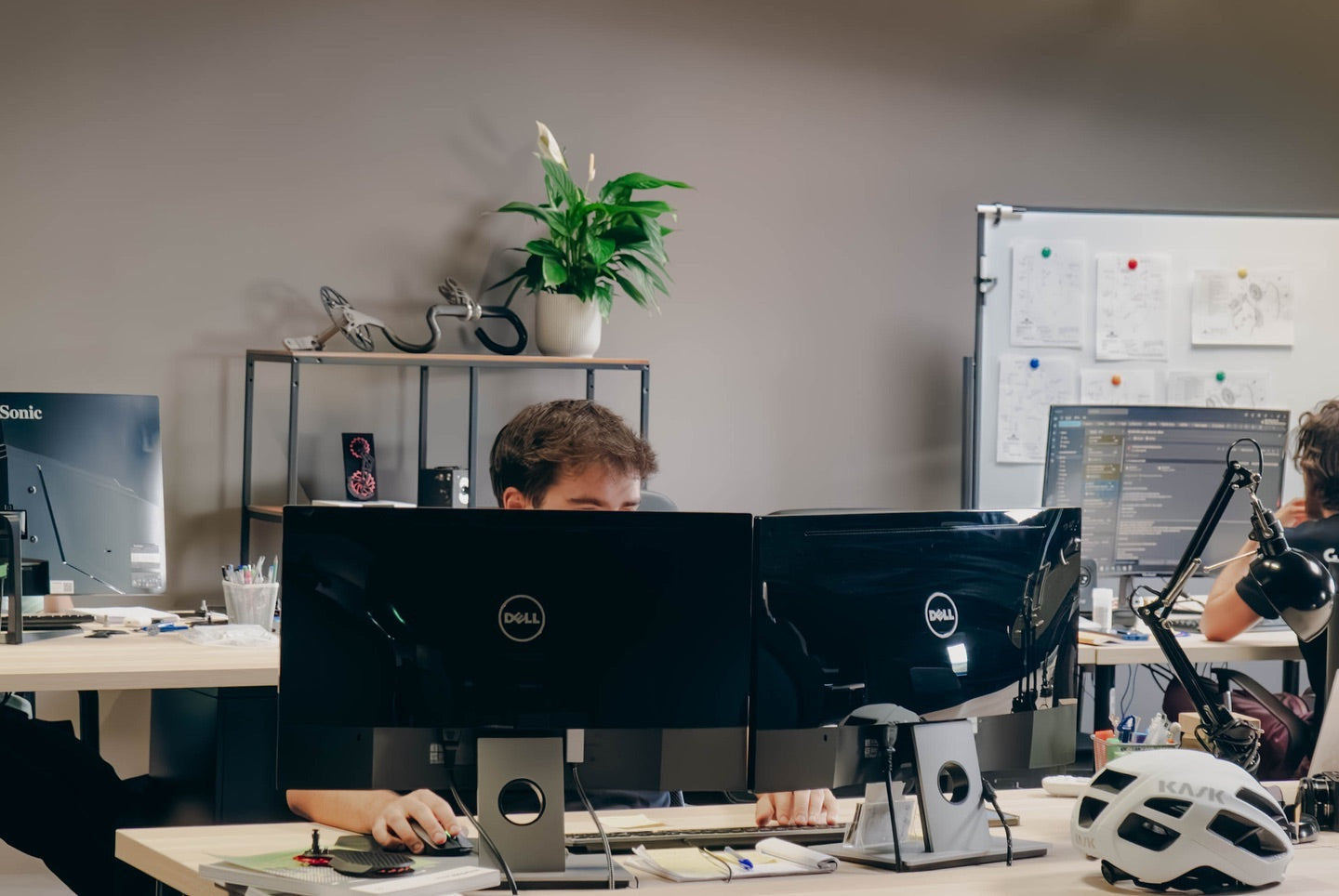
From the idea to your bike, there are many steps.
Ideation and 3D design
Pre-design is a crucial step for us. From idea to creation, these are iterative processes that require close collaboration between the different stakeholders in the project (engineers, designers, marketing, etc.). A component must not only be beautiful, it must meet a number of our criteria during its design: rigidity, performance, weight, durability, maintenance and cost.
In a second step, we use computer-aided design (CAD) software in the development of our components in order to move from the initial concept to its 3D modeling.
This software allows us to model our products, analyze their performance by simulating physical properties and performing resistance tests. We also use them to plan the industrialization of the part: by generating machining tool paths or 3D printing and other manufacturing processes.
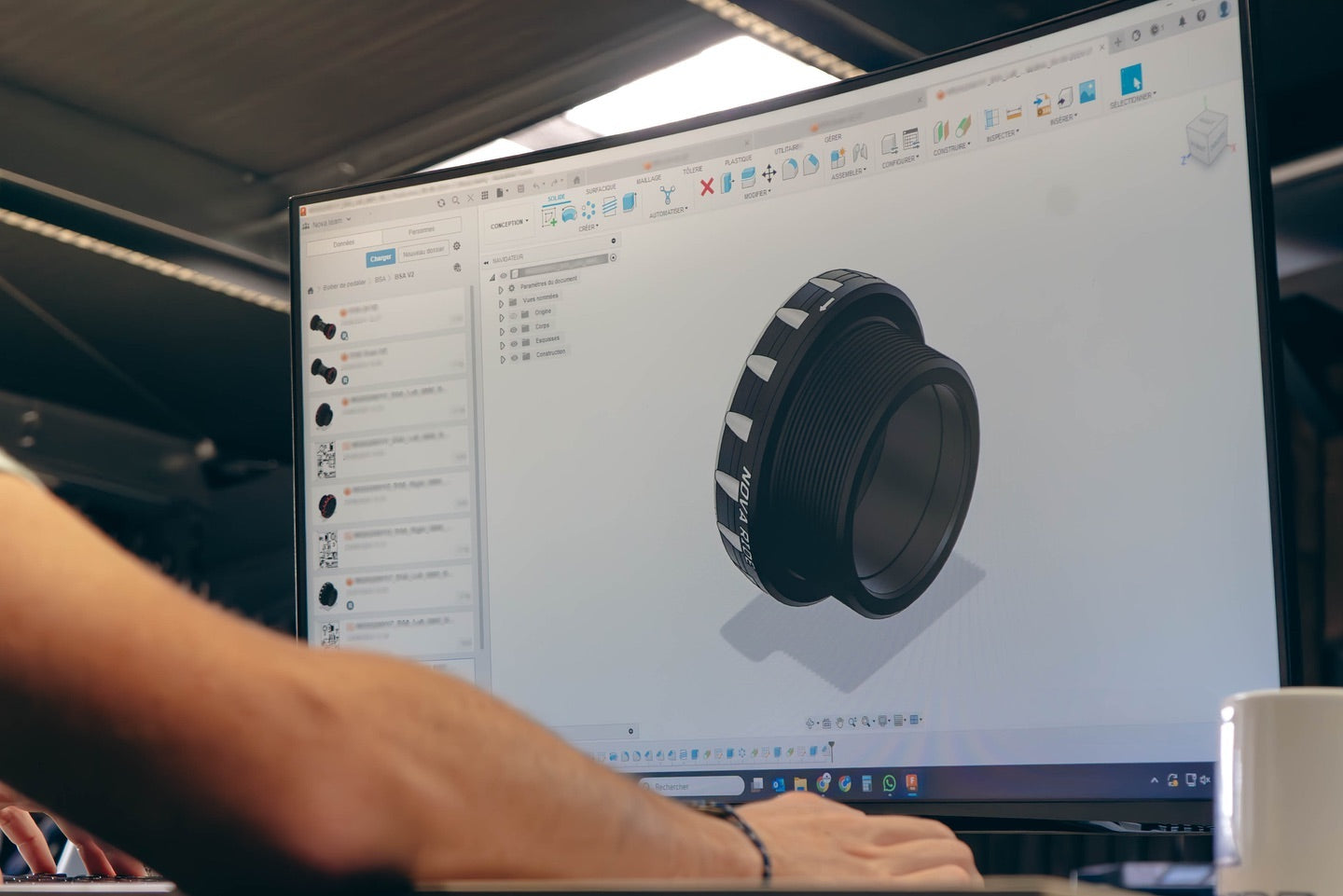
Prototyping and adjustments
We test, refine and adapt our ideas in real time. Prototyping fosters close collaboration between our team members. By visualizing ideas in the form of real prototypes or 3D printing, we can gather feedback from the earliest stages and thus co-create solutions that perfectly meet the expectations of enthusiasts and professionals.
100% Tested, 100% Guaranteed
From Design to Validation: Our Test Lab in Action
This is the part of our office where all our parts are subjected to stress and impact tests.
The test benches used are developed internally to meet our design and durability requirements. These requirements put the product to the test on shock resistance, fatigue and target stresses. We assemble and disassemble them according to our needs.
All these tests are compared with intensive and diverse field uses in order to guarantee the best quality to each of our customers. Once all of these tests have been validated, we move on to production.
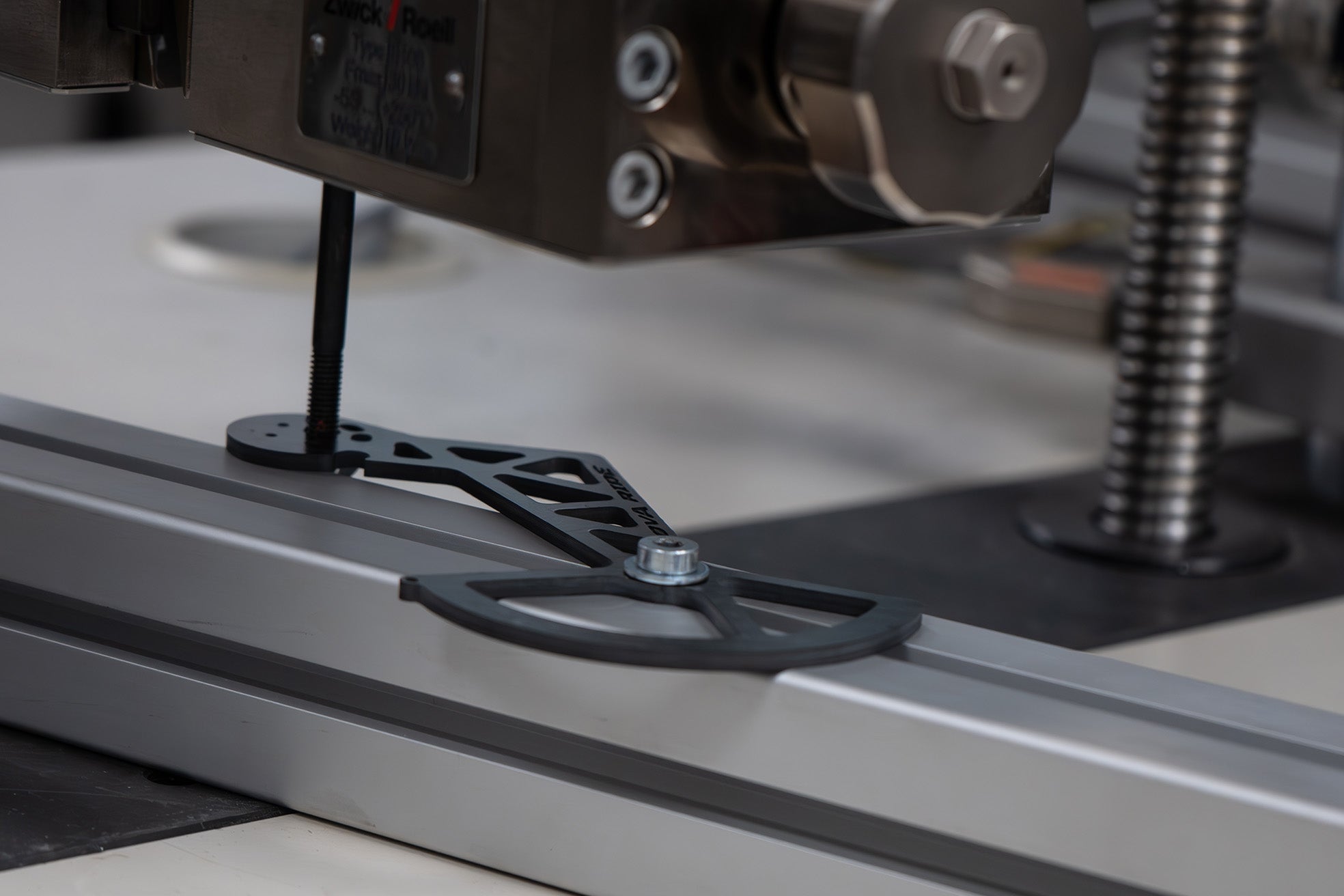
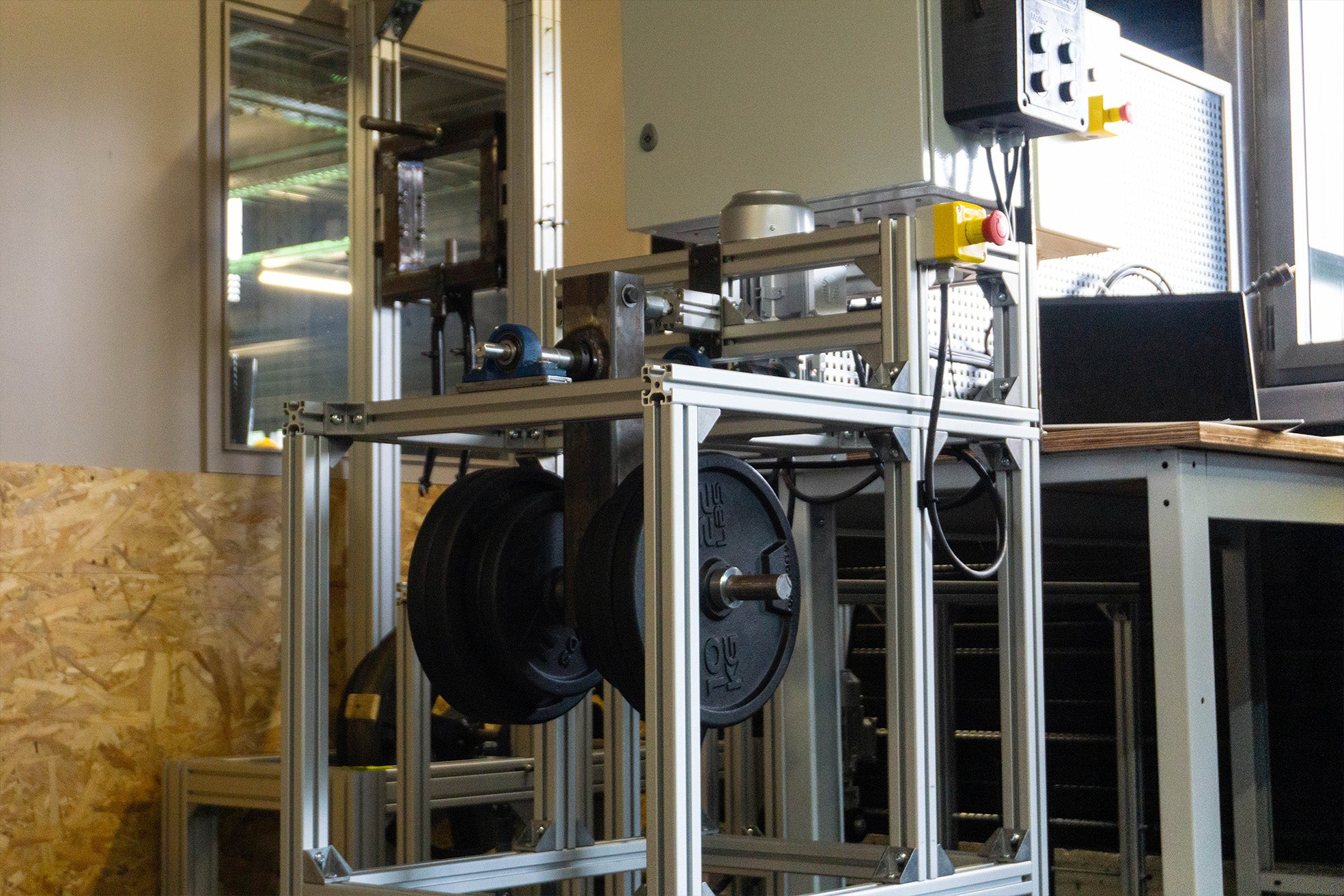
OUR PRODUCTION METHODS
As a small structure, in a context of continuous growth, we must optimize every moment of production. The challenge is to efficiently plan the manufacturing of our hundreds of references, minimizing machine downtime and avoiding stock shortages. A real challenge that we take up month after month.
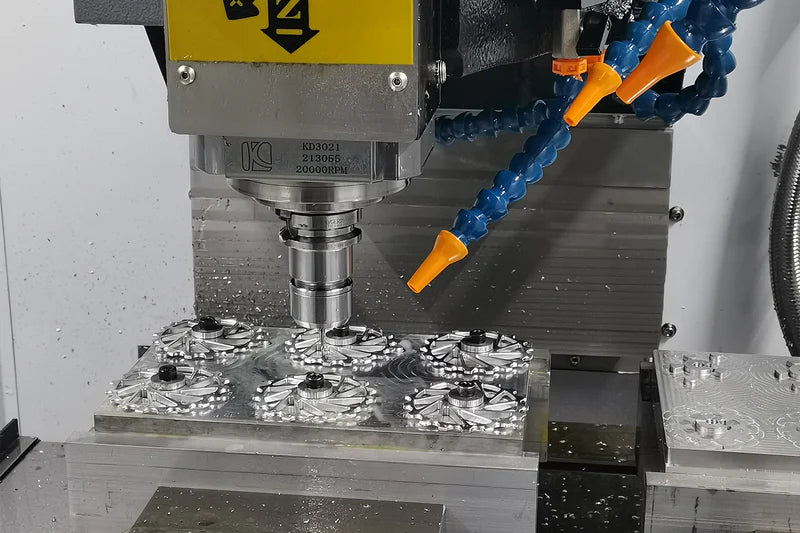

Machining
A meticulous choice of materials
We favor technical materials, such as 3K carbon fiber and 7075 aluminum alloy, recognized for their excellent weight, rigidity and durability ratio. These materials, which we master perfectly, allow us to design high-performance and durable products.
Precise and optimized machining
Each part is custom-machined to meet specific requirements. Thanks to digital simulations, we optimize the geometry and thickness of each component in order to obtain a perfect balance between lightness and strength. The shapes are carefully crafted to combine performance and aesthetics.
The advantages of carbon fiber and aluminum
3K carbon fiber, used in particular for our derailleur hangers, offers exceptional rigidity thanks to its specific braiding. The 7075 aluminum alloy, inherited from aeronautics, combines lightness, strength and ease of machining. It provides all the advantages of an aluminum material: corrosion resistance, easy to machine and lightweight while having remarkable mechanical behavior. The rollers, anodized for better wear resistance, complete the whole with elegance.
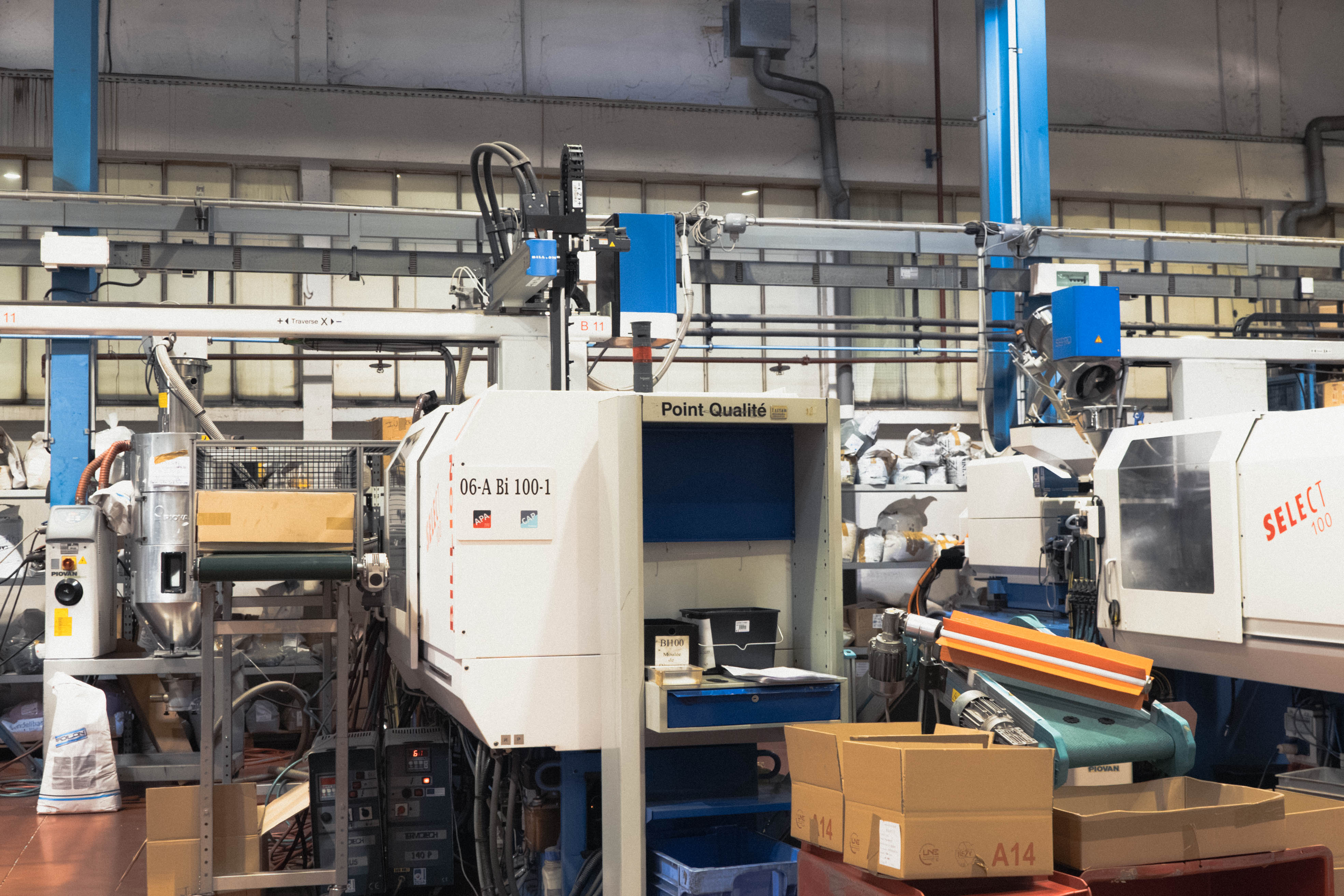
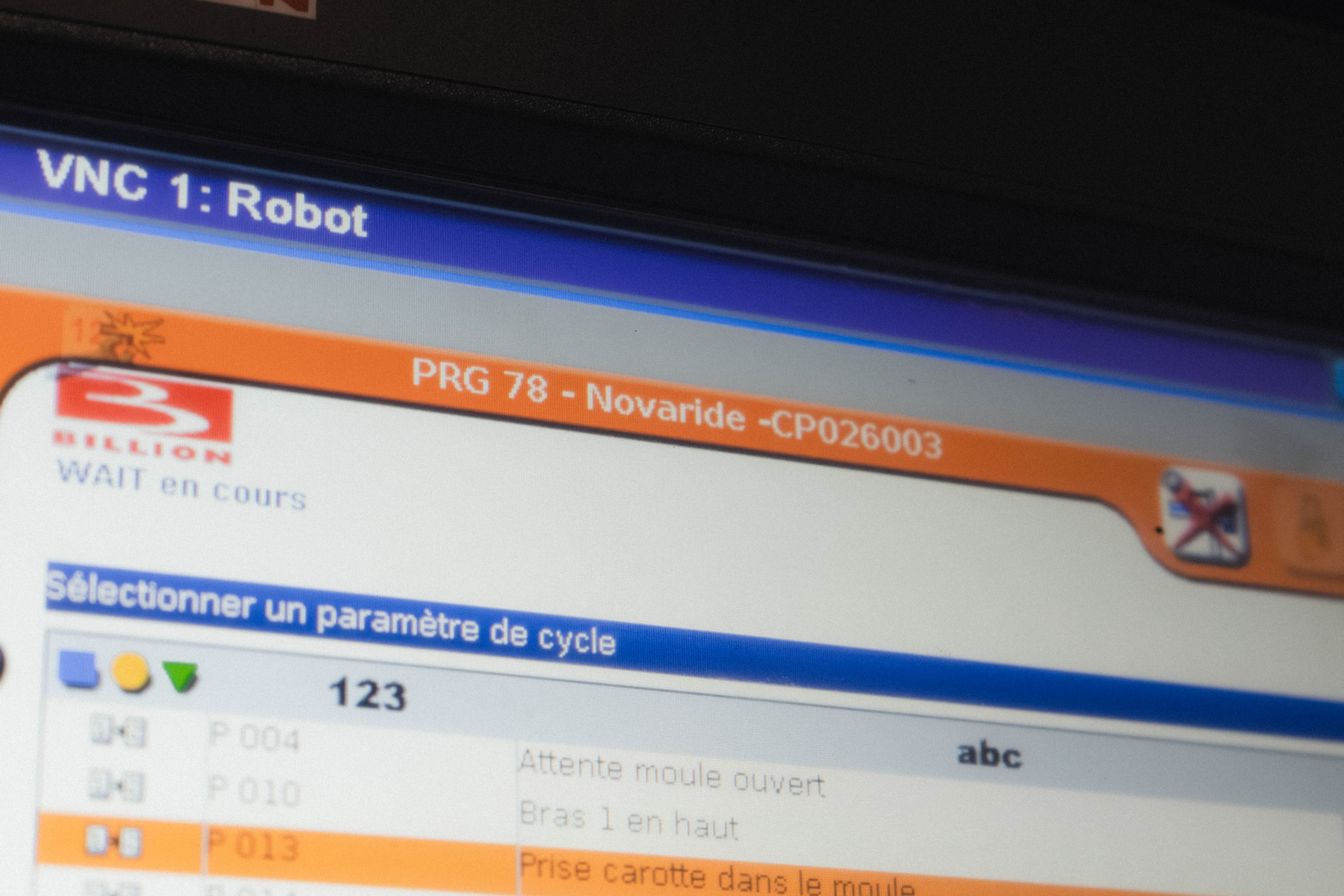
Injection
For some parts, we use injection methods to ensure precision and reliability in the repeatability of our productions. We have chosen plastic injection for our bottom bracket bearing covers and for our meter support adapters.
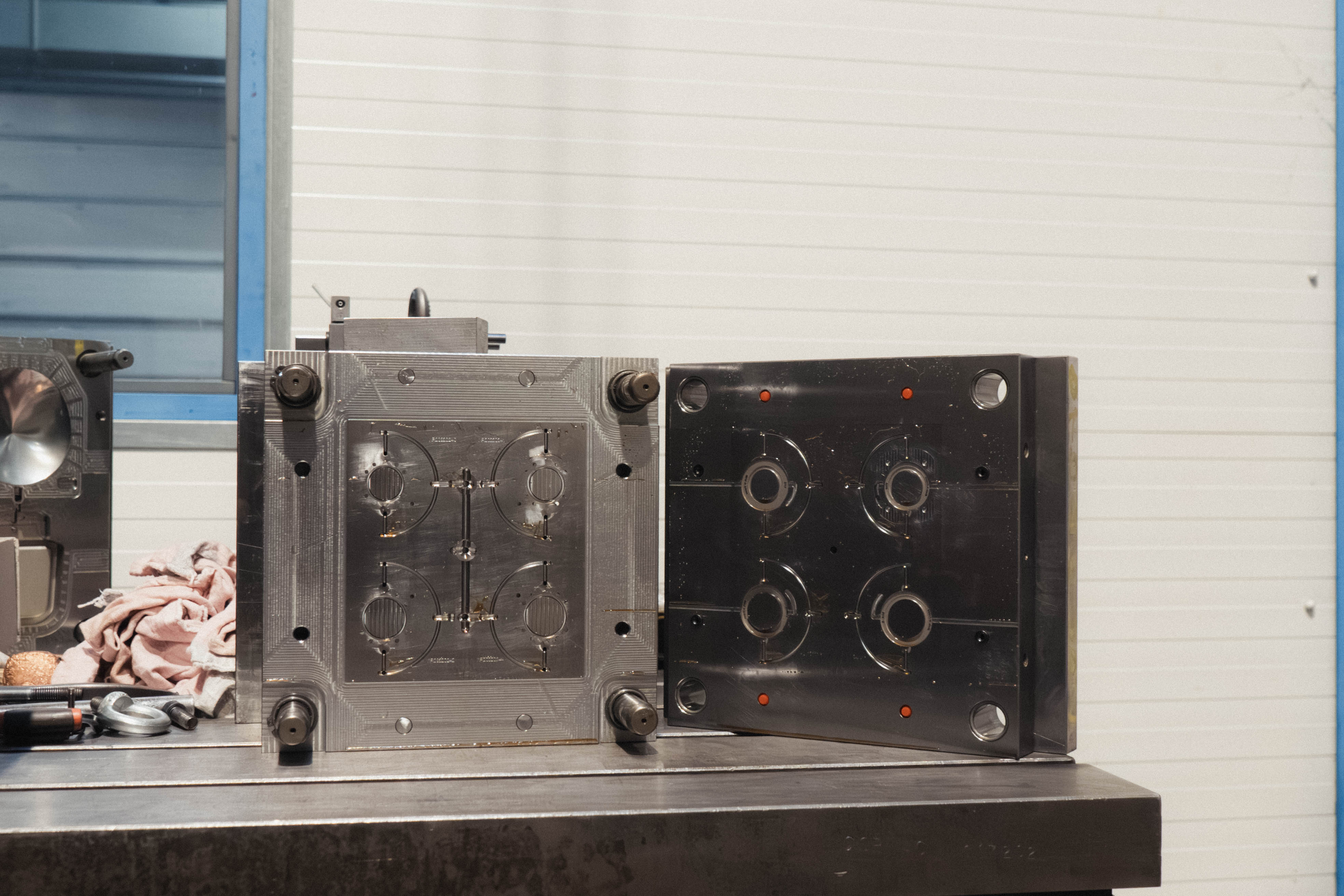
Quality control, assembly and shipping
We believe that every detail counts.
That's why all our orders are assembled in-house, where we oversee the quality control of each stage of the product's life, from materials to shipping.
Each order is unique. Our components are carefully assembled on demand in our premises and shipped within 24 to 48 hours worldwide in complete safety via our network of trusted partners.
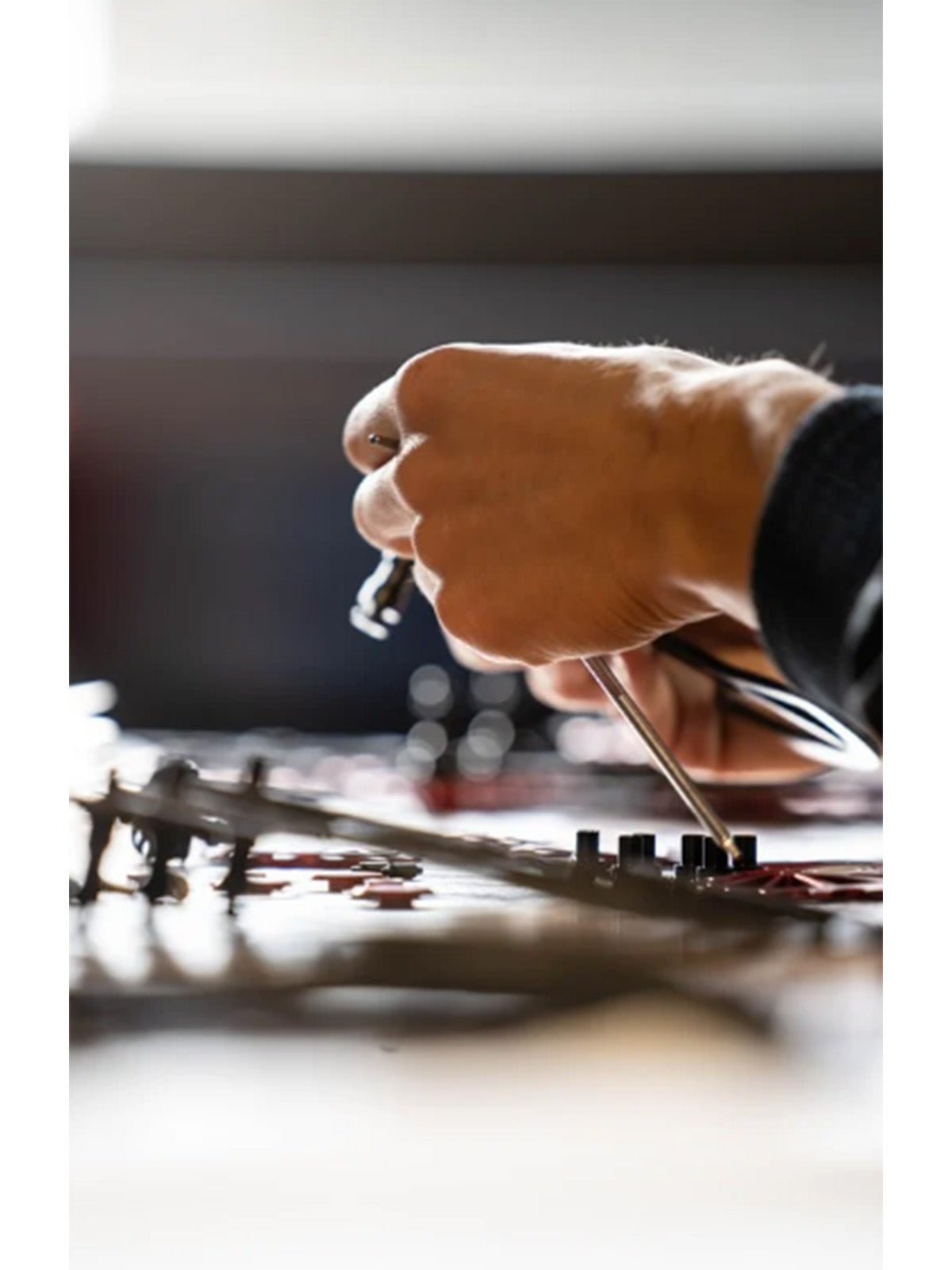
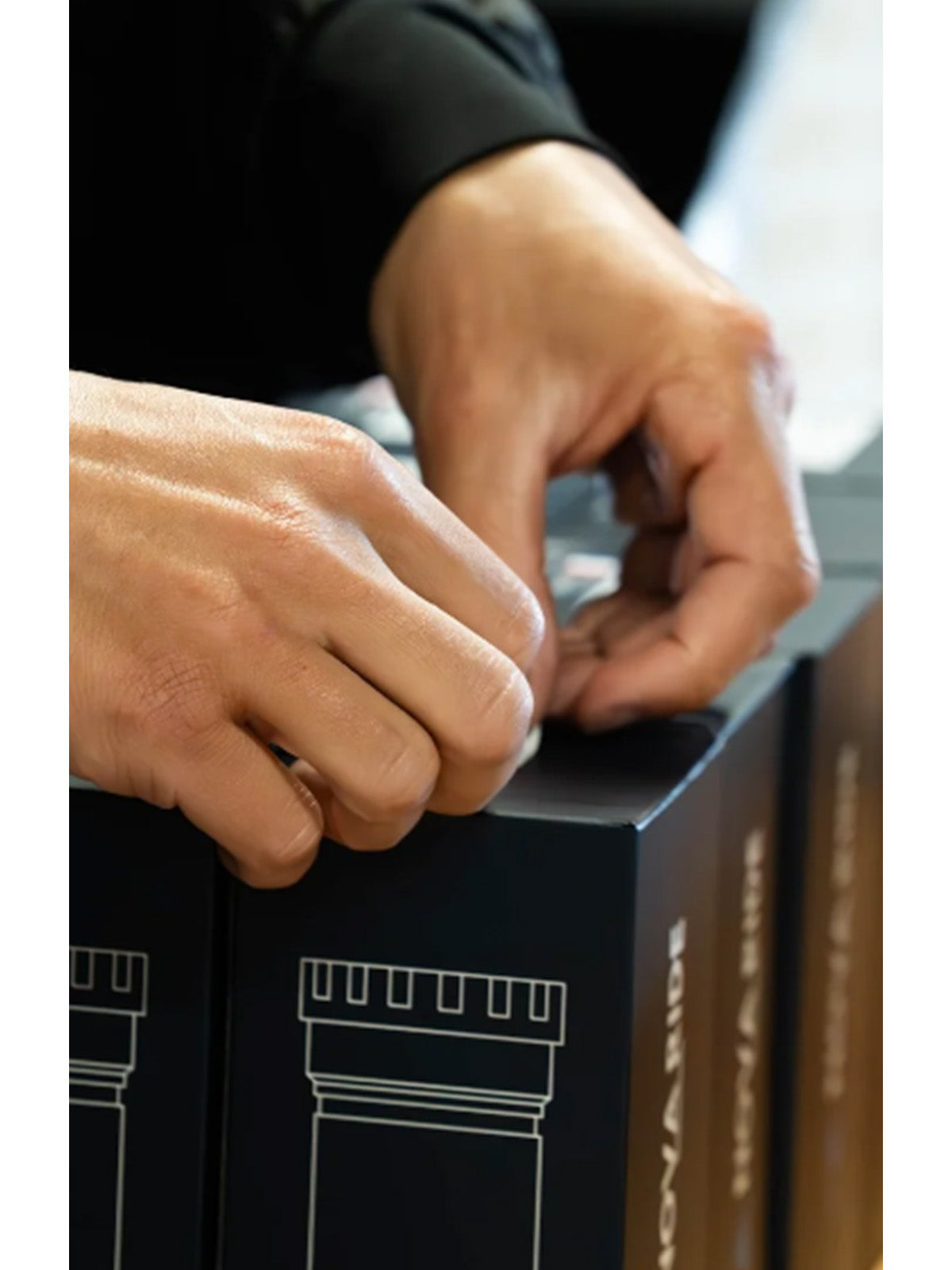
This page is updated regularly. We want to share our progress with you and show you behind the scenes of our work.